Heavy Mobile Equipment (HME) Superintendent
Location | Geita, Tanzania, United Republic of |
Date Posted | February 24, 2025 |
Category | Engineering Management |
Job Type | Full-time |
Currency | TZS |
Description
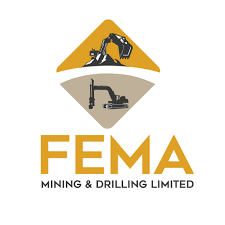
FEMA Mining and Drilling Limited is on the hunt for a HME Superintendent to join our mining business at Buckreef Site Project, working on 6weeks on and 2 weeks off roster from Katoro Geita Mwanza.
About Us:
FEMA Mining and Drilling Limited is a mining contractor of choice which employs more than 200 people across 2+ sites and delivers:
- Drilling and Blasting Service
- Load and Haul Services
- Tailings Construction Services
FEMA Mining and Drilling Limited is a company driven by its core values, we recognise that a diverse and inclusive work environment leads to increased engagement and trust, fresh perspectives and innovation and improves our overall performance. We see our people as our number one asset and understand that through our collective efforts and contributions we will be able to achieve our goals without compromising the health and safety of our people or the environment and communities in which we work.
The HME Superintendent The primary purpose of the position is to optimize the availability of mobile equipment by creating comprehensive and integrated work plans to achieve maintenance and service objectives, incorporating elements including routine servicing, preventative maintenance, major and minor repairs and overhauls, fleet commissioning, special projects, and related factors.
Key accountabilities:
General
- Establish and maintain Maintenance Planning standards and policies in conjunction with the Maintenance Superintendent.
- Conduct weekly planning meetings with maintenance and operations.
- Training and coaching planners in the preparation of work packages and all other planning functions for each maintenance work group within the organization.
- Organize in accordance with procedures external service provider’s visits to site for Condition monitoring and any other outsourced maintenance services not able to be done using on-site resources.
- Regularly review spares holding policy for maintenance spares and consumables and adjust the purchasing and inventory control settings as required to reduce reliance on airfreight.
- Attend regular meetings with operations and maintenance personnel to review equipment performance, develop remedial actions and improvement plans for cost and performance.
- Assist in the development of the departmental budget, with particular effort towards producing a Zero-based maintenance budget.
- Record Meeting minutes which include a list of actions and responsible persons and timelines for action when required.
- Develop a succession plan for all maintenance planning positions with clear competencies to be achieved and timelines for achievement.
- Work with the Project Superintendent to develop tracking and reporting systems for agreed KPI’s to allow accurate and quick analysis of maintenance, breakdowns, costs, and operating performance of all mobile and ancillary equipment.
- Improve reliability and equipment health through condition monitoring techniques.
- Participate in failure and damage reporting, tracking, work scopes and evaluations.
Safety Management
- Ensure all activities are conducted in a safe and compliant manner following company policies and industry best practices.
- Liaise with environmental and community relations staff regarding issues, incidents, or non-compliance within the area of your responsibility.
Training and Development
- Ensure that skills transfer is done and recorded
- Motivate a workforce by experience, knowledge, and respect.
- Train and mentor current site personnel and ensure that individual development plans are in place.
Mobile Maintenance
- Ability to satisfactorily work with others respectfully and professionally in a team environment, and provide reasonable instructions, training, and supervision.
- This position requires a lead by example approach to ensure best practice solutions are implemented as a team effort to encourage growth within the organization.
- The equipment consists of regular mining equipment, facilities and infrastructure currently supporting workshop and infield repairs.
Cost
- Manage maintenance personnel, contractors, and equipment in the most cost-effective manner possible as requested.
- Manage budget allocations and expenses for mobile fleet maintenance, ensuring cost efficiency and timely adjustments.
Policy, Procedure and Process Development
- Ensure that all policies and strategies are clearly documented following best practice.
- Recommend improvements to any process that may lead to safer, more productive operations.
Skills, Knowledge & Experience
Education:
Knowledge, Training & Relevant experience:
- Trade qualified Diesel Fitter, Mechanical Trade OR Engineering Degree.
- 10 years’ experience in large scale mining environment including at least 5 years in senior maintenance planning roles.
- Considerable knowledge of all aspects of a large and diversified fleet of vehicle and equipment maintenance including the involved trades and sub-trades.
- Ability to devise specific maintenance, major overhaul and repair programs that are effective and within budget and to coordinate the administration of programs to minimize disruption to the fleet maintenance program.
Practical/Specialist Skills:
- Prior experience in all facets of Mobile equipment Maintenance.
- Proven track record for reliability and sustainable processes.
- Proficient in MS Office and MS Projects.
Applying Instructions
To apply, kindly send your resume in pdf to hr@femamining.co.tz